springbrook
New Member
When I first got this boat the bow had been split and a repair had been attempted with silicone. The boat weighed 155 lbs, (with every thing removed) then after pouring out the water. It went down to 145 llbs. I tipped it up for four days and sponged out at least a pint for every day.
Next was to cut a hole for a drying port
I was not expecting this insulation under the deck
The foam was wet on the top and the bottom ( did I memtion this 78 sat out side for 15 years hull up, so I cut it in half and was happy to find the center dry.
Well then I built this home made forced hot air dryer.
what do ya think of it
Thats were I stand this eveing
How long should I let the dryer run?
The exhaust is runing about 95 degrees
I turned it down it will run 105 on high
at 95 it turns itself on and off every 4-5 mins
I think I will let run all weekend and weigh it on Sunday night
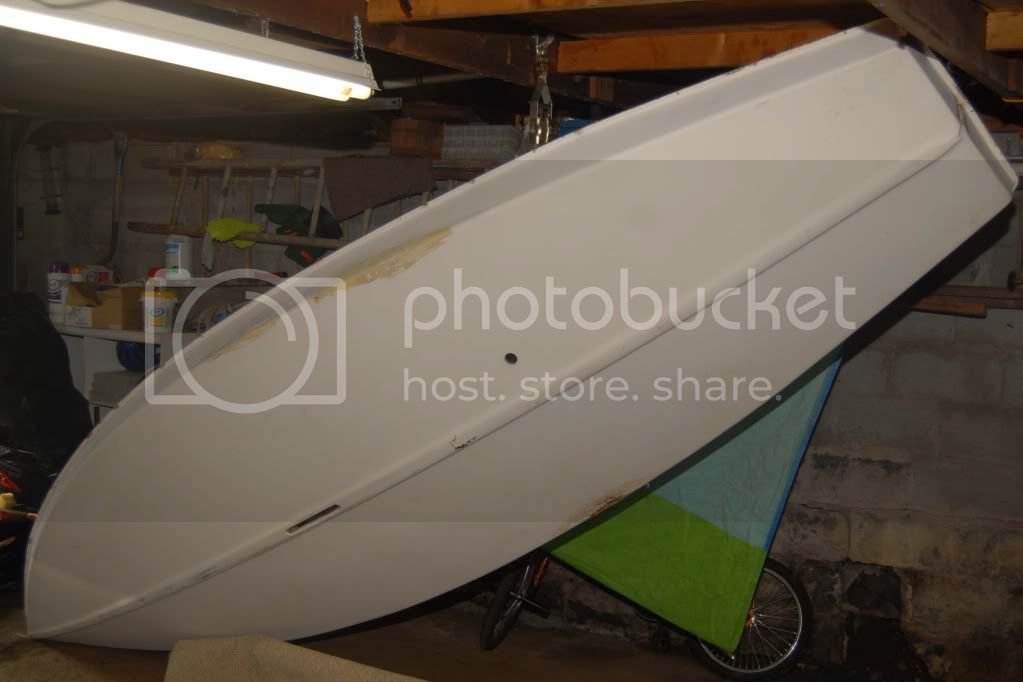
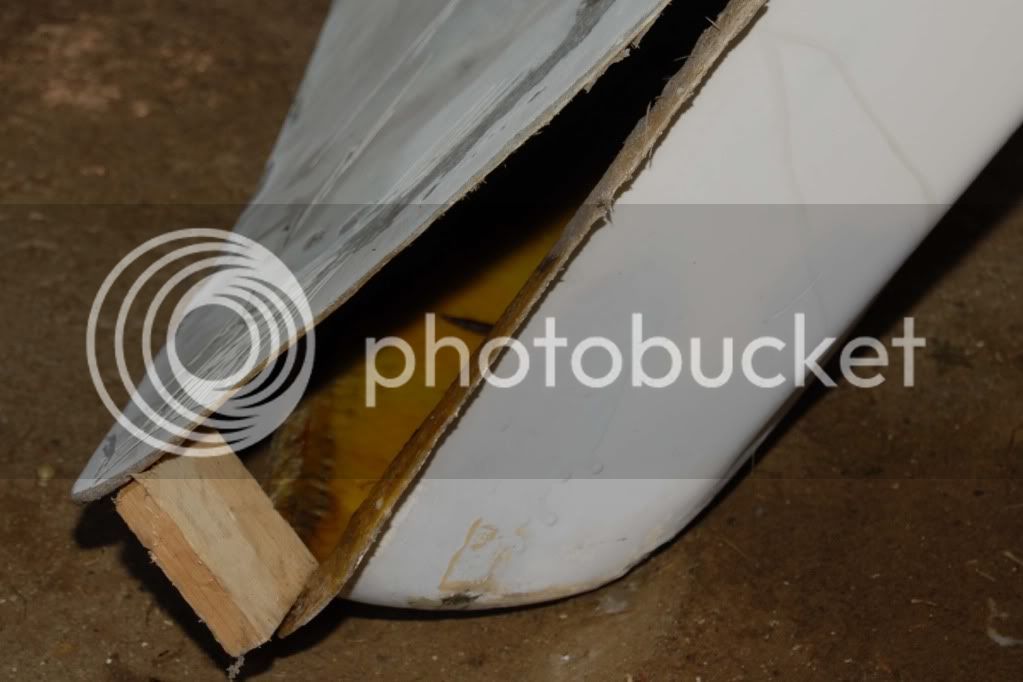
Next was to cut a hole for a drying port
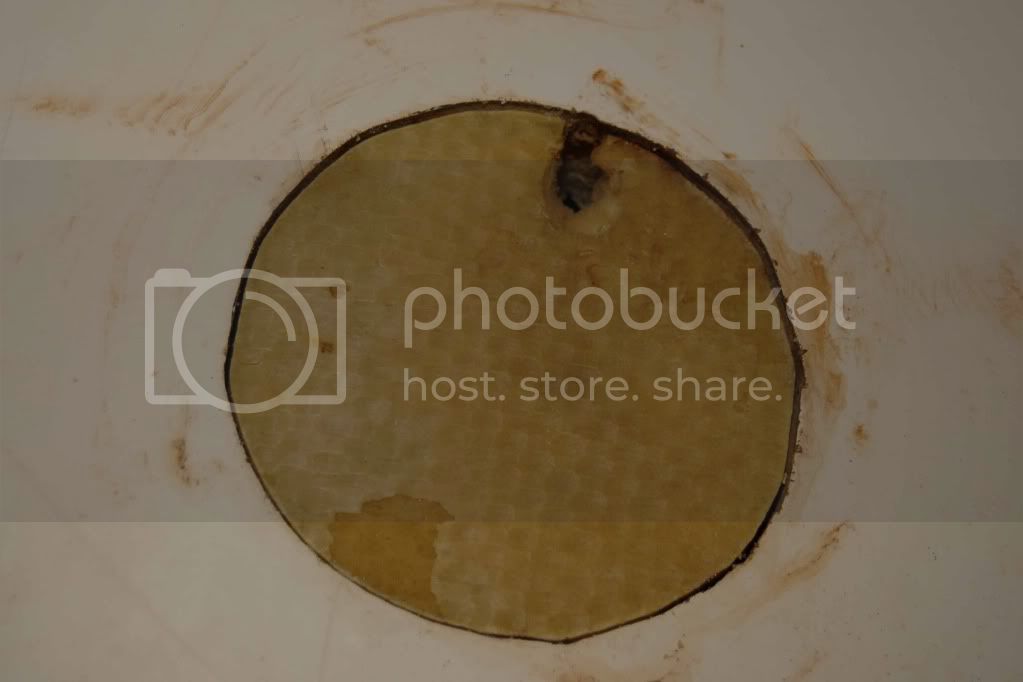
I was not expecting this insulation under the deck
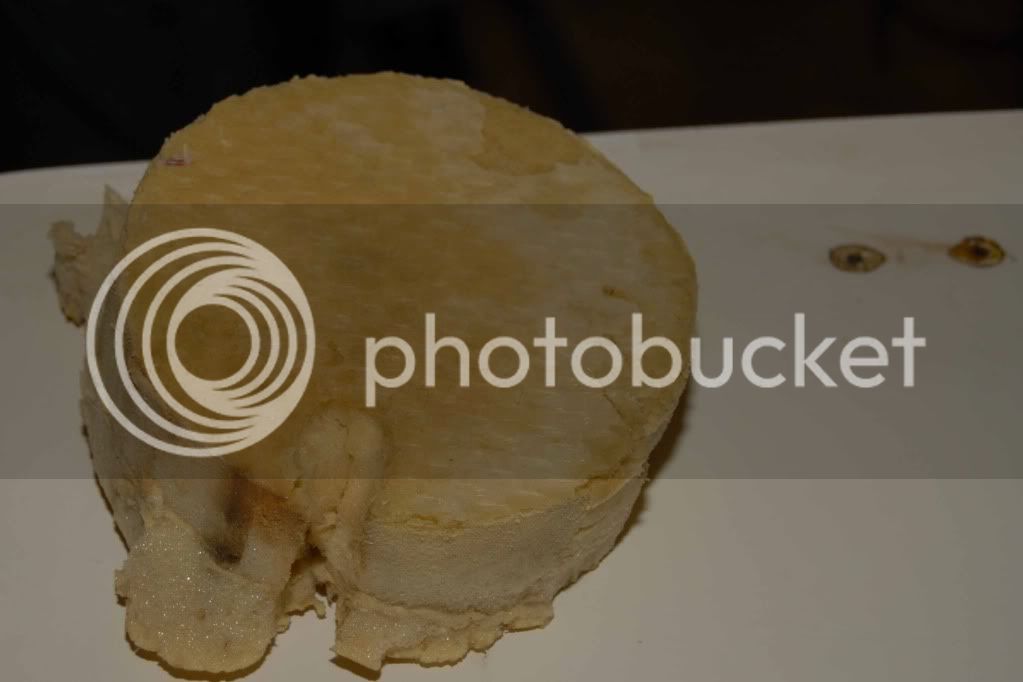
The foam was wet on the top and the bottom ( did I memtion this 78 sat out side for 15 years hull up, so I cut it in half and was happy to find the center dry.
Well then I built this home made forced hot air dryer.
what do ya think of it
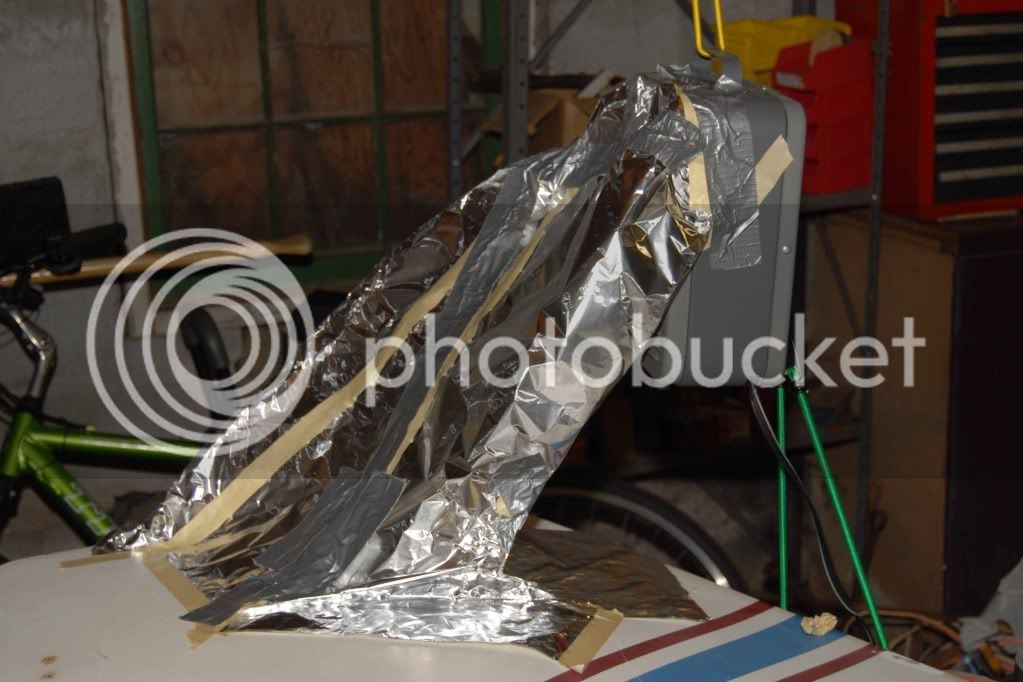
Thats were I stand this eveing
How long should I let the dryer run?
The exhaust is runing about 95 degrees
I turned it down it will run 105 on high
at 95 it turns itself on and off every 4-5 mins
I think I will let run all weekend and weigh it on Sunday night